Hello
I'm working on my second Greenland paddle, and that will be my first cedar one. I made a practice one out of white wood. I pretty much had zero wood working experience so I wanted some cheap wood.
It turned out better than expected but I can see that the tips will get chewed up. I know that I can use hardwood as tips so I bought some oak Tightbond 3.
The oak is only 3/4" so I guess I could shim it higher and glue it to the center of ends of the paddle but I'm really wondering what happens when the spokeshave or plane crosses over from the cedar to the oak? My white wood was cheap and had knots and the plane always chattered there. I didn't worry about since it was just a junk paddle but now I'm making the real one and the cedar/oak transition will probably be similar to planning over a knot.
So I thought I could do something like this:
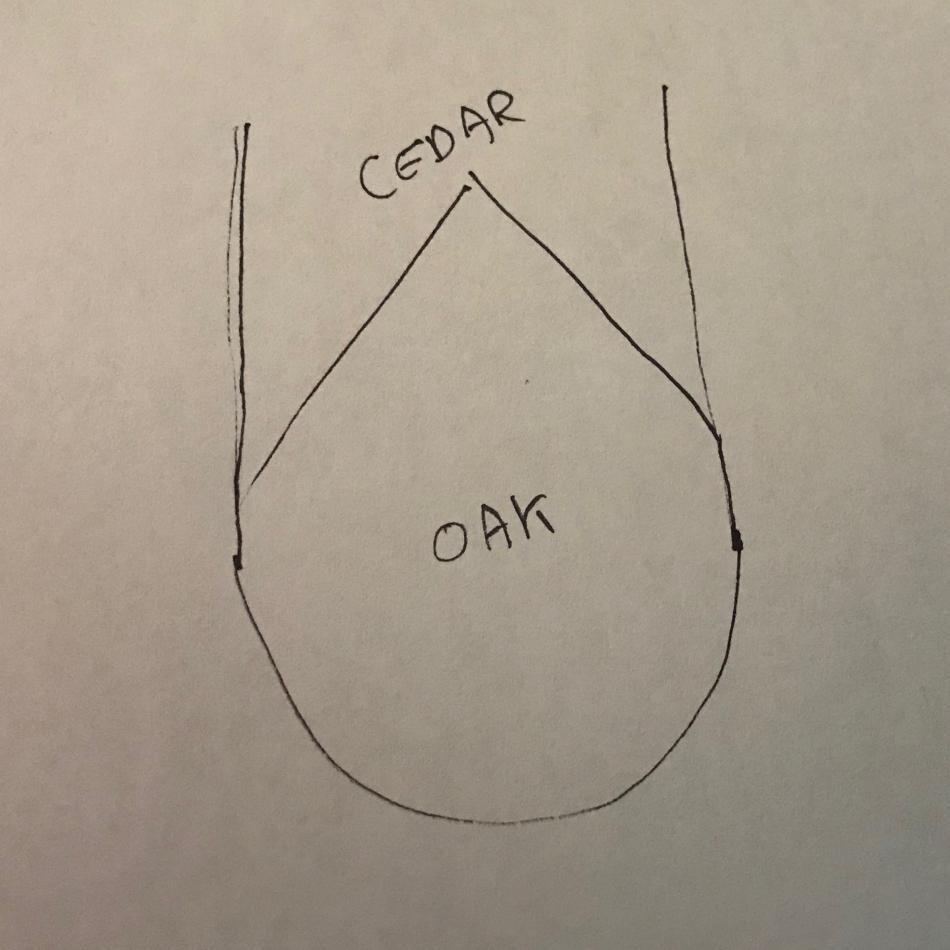
Is that going to making the planning easier? I'm pretty new to wood working, I'm also concerned about cutting the notch into the cedar with some precision. I can put the oak on the mitre saw and get a good clean angled cut, but I'll need to use a hand saw and then I guess files on the inner cut?
I appreciate any advice. Thanks!
I cant help you with oak but...
...have you thought of creating a blade tip using an epoxy/microbead mixture? The microbead/ expoxy mixture is very hard and resistant to damage. You could also probably color it with a pigment. I love the idea of wood/wood though. Just putting this alternative idea out there for you to think about.
I would reverse the angle on…
I would reverse the angle on the tip so the point of the cedar blade protrudes into the tip and the edges go farther down the sides of the blade. This would provide more protection for the high-wear areas of the blade, which is the reason for doing this in the first place, correct? It also eliminates having thin points of fragile cedar at the edges where the tip joins the blade. Speaking of which, although it would complicate the process a bit, you may want to consider squaring off the points and making them ~1/4" thick where the blade and tip meet at the edge, so you don't have any thin points of wood at the joint. Yet another option would be to add a 1/4" thick oak edge that extends down the blade an additional 12" or so.
I just realized I drew it…
I just realized I drew it backwards! Yes, certainly.
I like the idea of the squared tips, great idea, even though it won't be as nice looking.
As for the oak edge, that is probably beyond my skills at this point, I'm maxxed out on this!
No, but it is a neat idea. I…
No, but it is a neat idea. I do want to say with wood for now though.
Coating the tip with epoxy...
...is definitely the simpler process and it's what I do on my own paddles. I thicken it with fumed silica (like "Cabosil") and add white pigment. It makes a durable tip that is pretty easily renewed as it wears.
Oak edges...
...are actually much easier to do than the tips. If you're making a new paddle (rather than adding edges to an existing one), you can laminate the edges to the blank after you add the tips. You just need to make a recess for them in the edges of the blades. It will create the squared-off junction with the tips without having to do any complicated fitting.
There's a description of the process of adding edges on my book site: https://greenlandpaddlebook.com/Tips.html
GPs
Bryan Nystrom's book produces a beautifully shaped paddle, and will save you a lot of trial and error.
A paddle making workbench is handy too. I use bungee to hold it down while I am planing.
Et.
Padding on bench
Under carpet non-slip rubber padding on bench.
I put kwila tips on my…
I put kwila tips on my paddles. When you hit a rock you leave grooves in the rock - well not quite but yes, they are tough. The each tip has 3 of 3 mm Stainless Steel dowels and with 4 mm holes so no accuracy needed. The holes are filled with epoxy and the SS could be crimped by notching with side cutters or pliers.
https://canterburyseakayak.wordpress.com/greenland-paddle-make-your-own/
Timber Western Red Cedar, finished weight about 750 - 850 grams. Also note that by using a plank of wood 20 mm thick there is much less wastage than using a 2x4 "log".
My shafts / looms are rectangular as are those by some others. Yes, problems as one friend found out, she couldn't raise any blisters. Bend your second finger joint. It makes a right-angle. The upper hand - the push, base of the fingers against a flat surface.
That's a really nice…
That's a really nice workbench! Doesn't it move around when you plane? My workbench is ancient, it came with the house, and it wobble all over the place. I think your diagonal probably stops that. I should put some diagonals on the back.
Thanks for all the great…
Thanks for all the great advice and links! I like the idea of the edges, but I'm not sure I like the look of them. But it could be a case of form vs function also.
But back to my original question. Does the plane chatter and gouge if the transition from the cedar to the tip wood is not at an angle? I'm only seeing straight sided tips so it much be ok. Hmmm, I also seem to see people using sanders. I used a hand plane and spoke shave for almost my entire paddle. I only used a bit of sandpaper, going from 150, to 200 all the way up to 400. I did use a rasp on the shoulders but that took away too much wood, but that's my fault, not the rasp's!
Form AND function
Traditionally, Greenland paddles had bone tips and edges, which were definitely functional, but also added an interesting look. Adding contrasting tips and edges to modern paddles serves the same function.
Whether you'll be able to plane the tip-to-blade junction will largely depend on the grain of the tip. If you can't plane it without getting tear-out, you'll have to resort to a rasp, Microplane or sanding.
Wobbling bench
A couple of sandbags on the feet could hold it down, but I find a foot on the cross bar works fine if I need to push hard. If I was making another one I would put the cross bar lower. Maybe three inches off the floor.
Et.
Plane gouging
You mentioned you are a beginner woodworker. I assume you are using a low-angle plane for the finer cutting. If not, you should get one. You can go from a Stanley for around $40 to several hundred dollars. If you chatter one way, try the other way or rather than pushing parallel to the plane push with an angle attack at the wood joint. In-other-words, use the plane on a bit of an angle cut. Nothing wrong with grinding tools, sandpaper etc. if you need it.
Plane blade angles
Low-angle planes are actually designed for planing end grain. For dealing with tear-out and difficult grain, you actually need a higher angle on the plane iron. That's why smoothing planes have a higher angle than block planes, jack planes, etc. Those designed for really difficult grain have very high angles of 60 degrees or more.
The other thing that makes a big difference in reducing tear-out is the size of the mouth opening. The tighter it is, the better, while still allowing the shavings to pass through. So, a standard angle block plane with an adjustable mouth is the best way to go for reducing tear-out, short of using a smoother.
I forgot to mention...
...that I'd recommend getting a good-quality plane like those from Lee Valley/Veritas, Woodcraft/WoodRiver or Rockler/Bench Dog. They're moderately priced, have all the features you need, are precisely made and are usable out of the box with just a minor honing and mouth adjustment. Stanley's new "Sweetheart" block plane may fall into this category and you can get them at Home Depot for considerably less money.
High-end planes like Lie-Neilsen are a joy to use, but they're expensive and don't necessarily perform any better than those listed above.
Cheaper planes like the regular Stanley, Kunz, Groz, Anant and others require extensive tuning and sharpening in order to produce decent results and their blades don't hold an edge well. If you're going to put that much effort into getting a plane ready to use, a $10 vintage Stanley from a yard sale, Craigslist or Ebay will likely work better once it's restored.
Thanks for the updates. I…
Thanks for the updates. I should clarify a few things. Although I'm a beginning woodworker, my father in law is quite accomplished and has lent me his restored Stanley #4, which I've been using, his #3 which I'll use soon and the "I'm afraid to sharpen it because I might mess up its so gorgeous" Lie-Neilsen smoothing plane. There is also a 21" long Veritas plane, from looking at their web page this must be a jointer plane but I'm not sure.
Finally, I also have a collection of high quality spoke shaves from him. (He also has a Stanley #2 that he doesn't let me use!)
I'm able to sharpen the planes using his Veritas honing guide and I actually enjoy doing that, it is very contemplative.
The chattering I'm worried about is because I was using junk 2x4s, white wood, which had knots. Whenever I'd try to plane around the knots I'd get chatter. My fear was that when I transition from the cedar to the hardwood the same thing would happen.
And one more thing, yesterday he gave me a nice chuck of mahogany. Its from an old piece of furniture that was wrecked, somehow, and a friend gave him some pieces off of it. I've not measured it but I think it will be perfect for tips.
Depending on how much…
Depending on how much handwork you plan on doing, you may find the #3  useful, but you'll likely still want a block plane for the smaller tasks associated with paddle making. The jointer isn't likely to be of much use and it's a lot of plane to move around (I have one, but have never used it on a paddle). Spokeshaves are extremely useful and I use them much more than planes. They require more technique to use, but it's not difficult to get the hang of it.
Getting chatter in junk wood doesn't really mean much, as knots and their surrounding grain are a problem no matter how good your tools are. Try to find a piece of straight-grained wood to practice on (clear pine is fine), then spend some time with the tools until you feel comfortable with them. Spend some time looking carefully at the grain from multiple angle and testing what happens when you plane from different directions. This will give you a feel for what to do if/when you encounter any issues while making paddles.
Also, make sure that you're not trying to hog off too much material with each pass. The shavings should be very thin, on the order of .003"-.006". If you need to take off a lot of material, there are better tools for the job (saws, rasps, etc.). Planes and spokeshaves are for fine shaping and finishing. Since it sounds like you have multiple 'shaves, set one for a fine cut and another one for a slightly coarser cut. Use the latter for initial shaping and the former for fine-tuning. Remember that the more shaping you can do with your edged tools, the less sanding will be required to achieve the final shape.
When selecting wood for your paddles, I strongly recommend vertical-grain (a.k.a. "quarter sawn") wood. It produces a stronger, stiffer paddle than flat-sawn wood and I find it easier to shape and sand. It's not always easy to find, but it's worth the effort.
So I got some leftover…
So I got some leftover mahogany from my father-in-law and borrowed a neighbor and his table saw to both rip the cedar 2x4 and cut the mahogany into some tips for my wife's paddle.
But I want to go slow so I'm making a practice one first with the excess from her measured 2x4. I did the gluing today. I glued the mahogany.
Then I clamped 2 3/8" shims, covered in wax paper, to center the mahogany and then used a rachet strap for clamping force.
I let it dry for a few hours, it looks great!
Next I glued a white wood 2x4 to the cedar just so I'll be able to clamp it to my workbench!
Now if only this heat would break I can start planing. Actually, I have a floor clamp so I might do this outside.
Wood tips
Are you planning to glass the paddle blades?
Or adding dowels or some other reinforcement (metal dowels) to help keep the tips attached?
I don't know if you have a router, but there are possibilities for using a router jig so that you could laminate the added tip in place, mimicking a tenon.
End grain glue joints aren't very strong - try giving your test piece a good whack- the sort of thing that could happen if you hit a rock with the tip in mid-stroke.
I wasn't planning on…
I wasn't planning on glassing, nor epoxy. It sounds like I should?
No router. I do have a drill press but man, how do I get a tall piece into it?
I'll carve it then whack it.
Drill guide
I don't think glass is very traditional on Greenland sticks.
I do have a drill press but man, how do I get a tall piece into it?
If you are drilling for dowels, you can use the drill press to make a (wood) drill guide, to control the spacing and alignment of the holes.
Clamp the guide to the paddle parts and drill with a hand-held drill.
It's easier to do operations like drilling when the paddle blank is still a 'rectangular solid', IMO.
I like the idea of a drill…
I like the idea of a drill guide, thanks!
Why metal? Wooden dowels…
Why metal? Wooden dowels have the advantage of being easily shaped to fit the hole. And how wide should they be? The blade is about 1/2" thick at that point, would a 1/4" dowel really add strength? I guess metal would but then I'd also worry about exposing it accidentally when shaping.
I can't be the first person to do this.
Done before?
Perhaps you missed the post from Mac50L?
I put kwila tips on my paddles. When you hit a rock you leave grooves in the rock - well not quite but yes, they are tough. The each tip has 3 of 3 mm Stainless Steel dowels and with 4 mm holes so no accuracy needed. The holes are filled with epoxy and the SS could be crimped by notching with side cutters or pliers.
https://canterburyseakayak.wordpress.com/greenland-paddle-make-your-own/
The whole point of using dowels is to add long-grain glue area to a very weak end grain joint.
That's the idea behind mortise-and-tenon, biscuits and other types of wood joints. Woodworking 101 - though we can break a lot of those rules with epoxy and glass, we still need to pay attention! :)
Protecting the edge
Nick does an interesting epoxy and cord rim but he epoxies and FG the paddle. I have a white cedar greenland paddle that i really enjoy using, can't even imagine using a euro paddle. I don't hit too many rocks with my paddle but it does become a little scuffed. I use Watco teak oil on my paddle and it works fantastic. Touches right up with a little sanding and is UV resistant. I put 3 coats on and do a light finish sand with 240 or higher. Not too sure your end grain glue joint will hold with out plugs as previously mentioned. Good Luck.
I finally got around to…
I finally got around to doing a rough shaping, the weather has just been so nice I've been out paddling instead!
I rounded the tips and sanded, going from 80 to 320. Both the cedar and the mahogany looked great. But, I hadn't narrowed the blade at all so it looked dumb, plus I hadn't shaved nearly enough wood away. So I shaped some more. Here's how they look. I didn't bother to sand since the purpose of this test was to practice with the spoke shave and planes.
And here's the other side. …
And here's the other side. (the forum got weird when I tried to upload both)
All in all it was a pretty…
All in all it was a pretty positive experience. I do wish my mahogany was a little thicker. When I glued them together I had a slight bend so when I shaped them I had to take a lot off of one side and very little off the other. But that's the size of the piece I have!
I'm going to use metal dowels on the real paddle, I guess I don't need to glue them, just press fit them. I have 1/4" aluminum in my basement and other sizes are readily available. I think going larger would be risky since if I drilled poorly the metal could be exposed, plus I want some wood to be present to be strong for the wood. How long should they be? I'm thinking 3 inches.
Judging by the pictures, it…
Judging by the pictures, it appears that your tools are probably dull and you attempted to plane against the grain. It's very important that your tools are literally "shaving sharp" and you need to read the grain of the wood carefully. If you start getting tear-out, you have to plane in a different direction. It's not uncommon to have to plane the two sides of a paddle blade in opposite directions. When you add a tip, the grain is unlikely to to match the rest of the blade, which makes it difficult to shape with edged tools, since you may get tear-out on on the tip even if the blade planes smoothly. You may have to switch to using a rasp or Microplane for rough shaping and a lot of sanding in order to get a smooth surface.
If the piece shown is just for testing, try pushing on it to see how solid the bond is. Don't be surprised if the tip snaps off with relatively little pressure.
The reasons for using 3 mm…
The reasons for using 3 mm stainless steel dowels is they can be thin and strong plus the holes (4 mm) can be inaccurately drilled yet still get a fit. A bit of crimp on the dowels and epoxy to fill the holes and hold the dowels. Yes, epoxy might hold the tips on but with stress often applied, a bit more strength is a good idea.
The suggestion of wooden dowels shows how little wood around them is left after drilling holes for them. Aluminium, soft and again size, versus 3 mm for SS.
Thank you John for explaining / mentioning my previous post about dowels and assembly.
Epic fail - but a think I see a fix
Its been awhile since I worked on this, too much time outdoors and less time in the workshop. But any, I decided to build a drill guide and put the tips on with dowels. Everything went easily, which I guess was a bad sign given the finished result.
My drill jig needs to hold at most a full size 2x4 and hold the tips for this specific paddle. So I make a box around a scrap 2x4
Finished outer guide.
Here's the mahogany tip nestled in the box, showing the size of the shims that are needed.
Shims cut to fit
Drilling the guide into a piece of 2x4 on my drill press to ensure that the drill is perpendicular.
continued in next post.
Epic fail part II
The drill guide in the outer box
Here you can see the tips shimmed from the rear with the drill guide installed in the front. Ready to drill? Nope, a quick test showed that the drill guide was slightly smaller than the piece of scrap I used to make the. I need 2 dimes to shim it tight. After I took the photo I realized I could center it better with a dime on each side.
Epic fail - Part III
Drilling. There is still some side to side and up and down slop, but not too much. (That's called foreshadowing...)
Finished holes!
Now I attached the drill guide to the cedar 2x4. You can't tell but it is shimmed in the rear with the same side shims I used for the tips. Both the cedar and mahogany are 2 3/4" to fit the paddler's hand.
Dowels installed in the tips.
Glued and clamped. I did need to hammer it home some.
Yeah, the fail is obvious to me now but I didn't see it yesterday.
Epic Fail - Finale
You can see the horrid twist in the wood. This is not salvageable. I can't believe I didn't notice it yesterday. I can think of two solutions.
I could use 2x4 sized tips or I could use holes larger than the dowels and fill the gaps with sawdust and epoxy (or glue?) The later would let me eyeball it and remove any twist. I can probably even hacksaw this piece off drill out the aluminum dowels but that sounds like an awful lot of work with not much benefit.
I can hopefully take the cedar blank and make a storm paddle out of it, but it may be too short for me. But it should work out well for my wife, she's the one I'm making the paddle for anyways. I guess she might get two paddles out of it!
I'd take a chisel and split…
I'd take a chisel and split off the tip (avoiding the aluminum dowels).
Then heat up each dowel and pull them out.
Dowel centers would be…
Dowel centers would be another (possibly faster?) approach, though it looks like your jig got the holes drilled correctly.
For a good bond with epoxy,…
For a good bond with epoxy, I find that it's better to rough up the surfaces and not have a too-tight fit.
For gluing alignment, you could hot glue blocks to the tip to make the overall size similar to the paddle blank (2x4?).
Then you could clamp a short board to the paddle blank and the tip block to keep them lined up while the epoxy cures.
You can definitely fix this…
You can definitely fix this.
You can just take the tip off and re-do.
If you did need to make the paddle longer, there are lots of good ways to do that if you are gluing long grain to long grain.
(Scarfing, fishmouth, tenon, etc..)
It's trying to glue end grain to end grain that is problematic.
Dowel center jig
This is the jig I use to center dowel holes on wood. Works just as well on end or edge grains and thicknesses up to 2". I has drill bushings for 3/16" - 1/4" - 5/16" - 3/8" - 7/16" and 1/2" I worked with the designer for many years and have one of his original designs that is still totally accurate after 4o years of use. Available on Amazon $45 plus several other sites.
Wow, thanks for all the…
Wow, thanks for all the advice! I think I cut off the cedar and chisel out the dowels. I'd rather save the mahogany than the cedar. I don't have much of that. That metal jig that Randy posted looks just about perfect. I still wonder if I'd get my drill in crooked, but since it isn't made of wood that seems less likely.
I think I will oversize the holes somehow. It all depends on what size that jig comes in and what size dowels come in.
My birthday is the end of the month, and then Christmas, gifting hints have already been given... :- )
My usual paddle end
Don't over analyze this chore. make a card stock template and cut it out with a jig saw.
use darkened epoxy to attach it in, make it thicker than you need if the paddle is shaped. Then jus shave it down. Mine is Mahogany on a pine paddle.
Jay's example is excellent,…
Jay's example is excellent, IMO -
It looks great and has good long-grain gluing surfaces.
For pushing ice out of the way when seal hunting, you could consider (pinned) bone tips for your paddle.
:)