Forums
I was reading the caption on Etienne Miller's photo which said that he was wetting out the deck and using that cloth overhang to join the deck to hull. Maybe this the way to go? Sand and glass the underside first. It would necessitate a perfect fit without the usual forcing we go through with packing tape. Maybe Etienne you can comment on that. I kept thinking about the logical steps.
Without female molds to rest…
Best on stitch and glue
This works great on stitch and glue, not as good on strip built. You can still do the force and tape thing. You force and tape and fill the seam with thickened epoxy using a dental syringe and then clean it all up before you glass. I have done it with a strip built but there are two significant challenges. For me the biggest challenge is the deck is very tender and easy to break if you do not have female molds while sanding and glassing. As John mentioned above keeping the shape can be an issue, I just put shrink wrap over my cross sections and around the edges of the hull and put the deck back on the forms when it was partially cured and taped it down so it would hold shape. The third issue is I like doing the hatches and the cockpit while the deck is off the boat and after it is glassed.
Hull to Deck
I am an advocate to the E.Muller Method of joining the Deck to the hull. I carefully fiberglass the underside of the deck after the fittings and hatch mounts are in place. It is much easier to align the deck to the hull with only one side of the deck being glassed. The inside joint is fiberglassed first then the deck gets fiberglassed with an inch and a half of cloth overlap on to the hull. This will make for a lighter weight joint and eliminate separately taping this joint.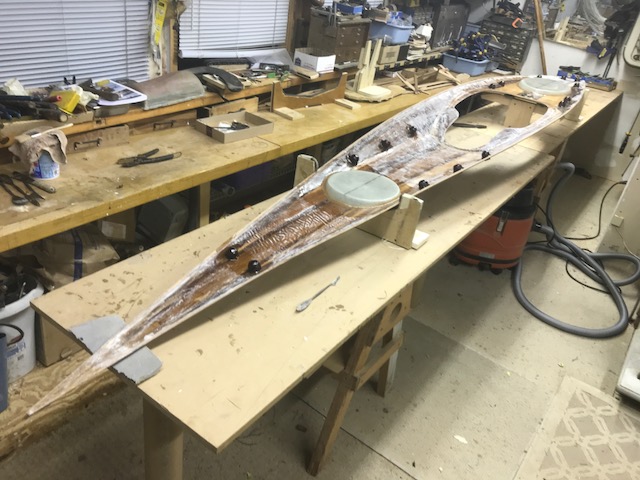
hull deck
additional photo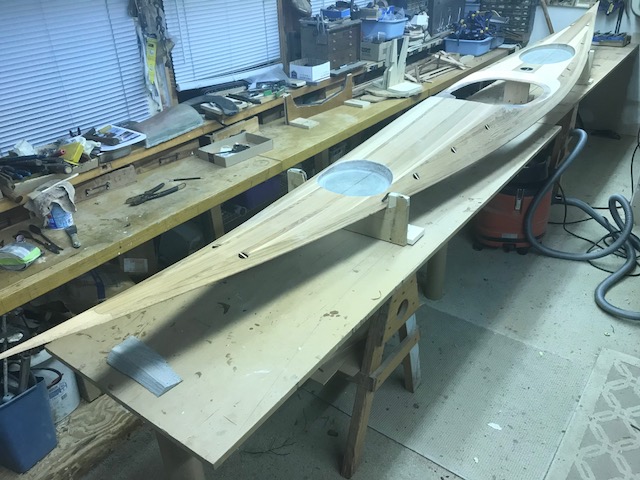
hull deck
there must be a way of posting more photos in one comment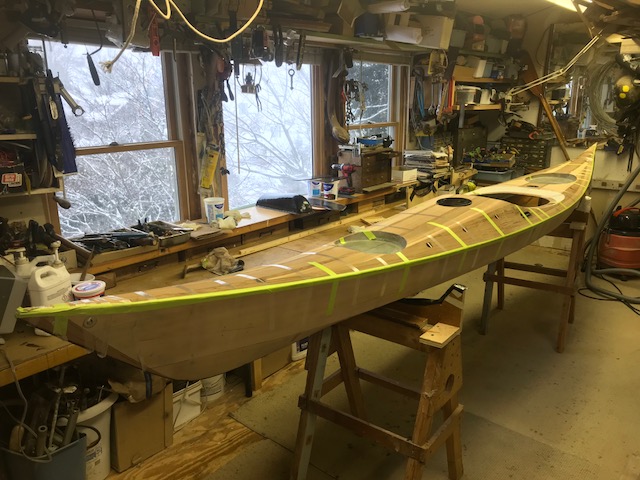
hull deck
Al last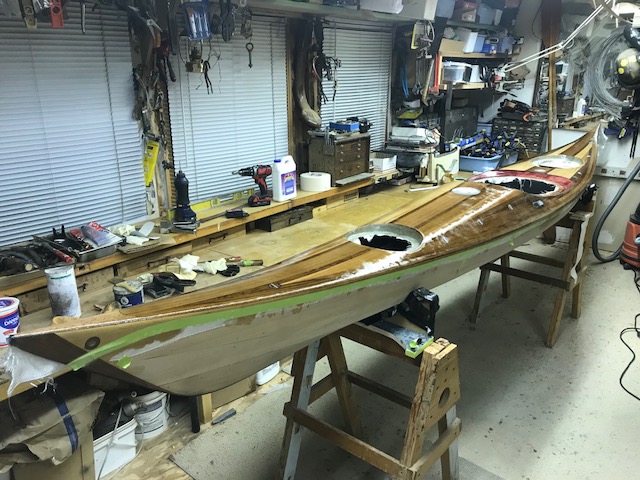
Hull deck
like Bob, I also only use two cradles to hold my deck while I glass the underside. If the deck has a lot of curve in it its is not necessary to support the ends. If it is fairly flat, as rear decks can be, a bit of support at the ends gives confidence. I use pool noodles cut to an appropriate length to support the ends. See photo.
It is true that close fitting joints help with structural integrity, but once it is in the cradles it can take more hammering than one might think.
I enlarge the opening for the cockpit just before I actually glue the deck to the hull, as the narrow sides at the cockpit are the weak spot. So far, I have also cut my hatches after glassing the outside, as I use the hatch cutouts for lids, and if they are glassed separately to the rest of the deck there is a risk that they may distort differently to the deck as the epoxy sets up and will not conform perfectly to the same curve as the deck. Obviously this is not a problem if plastic hatch rims are to be fitted.
Here is a public access link to my latest boat, which shows the process in fairly good detail.
https://www.facebook.com/media/set/?set=a.1333322866728523.1073741835.1…
Hull deck
As Bob notes, the deck will be much more flexible before it has been glassed on the outside, alleviating one of the known frustrations of bonding the two halves.
I should perhaps have mentioned that I use straps on sawhorse cradles to hold the deck while I scrape and sand it, partly to keep sanding dust out of my glassing area, but also so that I don't have to keep swapping hull and deck cradles on the strong back, as the hull is already in its cradles and would need to go back in again when the deck is joined to it. I also fit all the maroskes, on the saw horse cradles.
The only reason I ended up doing the deck glassing this way is that I started stripping before the advent to the Internet, and all the current information was not available. I just did what seemed logical steps on my first boat, and have been more or less doing it ever since. I think the literature, plans etc that came out over the years has mostly instructed builders to glass both sides before joining, and it just became common practice.
There are a few good reasons for glassing both sides first: it is safe to cut out the hatch lids without having them distort differently to the deck, which means you can work on hatch lips from underneath more easily, and also get in to tape the inside sheer at the ends more easily. If you have bulkheads fitted already, this would have to be done after the deck is joined and they are cut out, as there is no access. With sheerclamps this is not an issue, but not all boats are conducive to sheerclamps.
The second reason is if you intend doing something fancy with cockpit recesses and you need to be able to work comfortable from the underneath again.
Hull deck
Hull deck
Hull deck
All the under deck stuff went in before fitting the deck to the hull and sanding and glassing the outside.
Masking the hull prior to glassing and joining the deck
Ready for glassing the outside.
Under deck storage
ET what are the dimensions of your under deck storage and would you make it any larger or smaller if you were to do it again?
Makeup compartment dimensions
Makeup compartment pics
Makeup compartment pics
Makeup compartment pics
From below
From above
Closed
Etienne, I really like the…
Etienne,
I really like the way you tied off the bungee in the last picture, that's a great idea. I've just installed Maroske fittings on my kayak this week. This eliminates the knot at the center gives a bit more space between the bungee and the coaming.
strip pinning
Etienne,
Well, as warned when you welcomed an ex-lurker onto the new site, there "might be a few" questions for this community of masters and enthusiasts. I've done a few S&G, but getting ready to do my first stripper. And even having seriously studied Uncles' Nick's and Rob's and Val's materials and hot glues and clamps and staples ... And OF COURSE staple less techniques - I rather like the neat rows of single pins you use (at least on the hull). Would you mind describing your technique for this? Tapping in lightly blunted brads, blocking up an air nailer, pre-drilling......? I lost 20% of strips (dues to saw, fence, blade, time of year, wool on the catapillars, lunar phase, sun spots, and improperly chilled beer), and don't want to see these split.
Scott
Strip pinning
hi Scott. I prefer pins, because one hole is better than two.
Look for veneer pins. You will find them on eBay if you can't get them locally. They are fairly thin, so do not leave a big hole. I don't blunt them. The cedar is soft enough that it won't split. I never had one even threaten to split on me.
Many planks and locations could do without the pins, but I put one in every plank for the sake of uniformity. It looks like a diliberate artefact of the construction that way. I try to keep them evenly spaced, and in a straight row.
I use a smallish hammer to drive them. When the plank is dry fitted, I drive pins into it, but not through it, in the appropriate spots, then remove it, apply glue, and then just move along tapping them in. I leave enough sticking out to be able to get pliers onto them for extraction.
Every now and then one wants to drive one all the way in to the head, in order to tame a wayward strip. In these cases I use a short piece of waste strip, an inch or two, as a spacer. I wrap it with packing tape so it won't stick to any glue squeeze out. This can be pulle off afterward, usually pulling the pin with it, or pulling over the head to allow room for pliers.
Et
Et - many thanks for the…
Et - many thanks for the reply and details. Have spent LOTS of time looking at your posts and thinking and figuring..... And then to simply ask?. Fun not to be lurking.